I swear I posted this thread on the forum before, however, I can't seem to find it, even when I search all of the posts I have made under my username.
In any case, I apologize if this is a repost. As of late, I've noticed a few threads discussing air compressors, piping, and in-line desiccant dryers (rustybronco). The following writeup is how I decided to tackle the issue of water in my compressed air system.
****
I have an Ingersoll Rand SS3L3 air compressor, 3hp/single stage/135psi/230V rated at 100% duty cycle.
Although the compressor can run continuously for long periods of time, by nature, the temperature of the air charge leaving the compressor head becomes scorching hot (225+ degrees F). Herein lies the problem - I often use my compressor for media blasting, and once the compressor runs for 15+ minutes, the air tank itself is hot to the touch. Once this hot air reaches the downstream air lines, the water immediately condenses out of the air and my blaster starts spraying a mixture of media and water. Finally, my blaster clogs and it becomes useless.
Simply installing a centrifugal water filter/separator before my hose reel proved to be insufficient due to the overall temperature of the air charge - by that point, it still had not cooled down enough to allow the water to condense out of the air.
To help mitigate this problem, I built an aftercooler for my compressor. In essence, this is a heat exchanger (radiator) that sits between the compressor head and the tank. Immediately downstream of the aftercooler is a centrifugal water filter/separator. The aftercooler works by lowering the temperature of the air charge to the point where the water condenses out of it and subsequently gets trapped by the separator. This allows (mostly) moisture-free air into the compressor tank. Whatever moisture isn't caught by the separator will condense in the tank itself because the temperature of the tank is now much cooler due to the fact that the incoming air charge is no longer scorching hot.
For parts, I used the following:
B&M plate/fin transmission cooler rated at 200psi (new, eBay)
Dayton 230V axial fan, 665cfm (used, eBay)
1/2 OD copper tube and Parker SAE 45 degree flare fittings and "long" nuts for plumbing (new, Home Depot and McMaster Carr)
A Norgren 3/4" NPT in/out 40micron filter separator with manual drain (new, eBay)
A cooler and fan mounting bracket - (built from scrap steel)
CDI 20cfm in-line check valve (new, eBay)
1 3/4" x 5/8" aluminum spacers for mounting the cooler to the bracket (new, McMaster Carr)
Miscellaneous nuts and bolts (stuff laying around, free)
The fan is wired in parallel with the compressor motor - when the motor turns on so does the fan. Also, I removed the tank-mounted check valve and installed a new compressor-rated check valve at the inlet to the cooler - I also relocated the pressure switch unloader line to the unloader port in this valve.This arrangement will keep the cooler and separator pressurized, and thus, the unloader will only be depressurizing the short run of copper line leading to the check valve. If the check valve is not relocated, every time the unloader opens it will be dumping all of the air in the cooler and the separator, causing your compressor to "hiss" for an unusually long time once the motor shuts off.
I also added a Solberg filter/silencer to the inlet of the compressor - this isn't critical, however, it quiets down the compressor and keeps the incoming air nice and clean. It's a much larger, more efficient unit than the dinky OEM filter.
Long story short, once I put everything together and got the system running, the decrease in output temperature is dramatic - after 15min, the copper line leaving the compressor head is so hot that you would not be able to touch it without receiving a nasty burn. By contrast, I can comfortably keep my hand on the copper line leaving the cooler.
I will verify the temperature drop with my IR temp gun when I have a bit more time, however, I am guessing there is at least a 150 degree difference.
The amount of water that the separator catches is also dramatic - after 15min of continuous running there is almost 3/8" to 1/2" of water in the bowl. This is water that ISN'T going into my tank and lines
For the record, I flared all of the copper lines using a 45 degree double-flare kit and I used Parker fittings with long nuts (better support for the tube end in applications with vibration). All of the pipe thread fittings were sealed with Permatex high-temp pipe sealant. Originally, I plumbed the entire system using Watts Ander-Lign compression fittings from Home Depot...... WHAT A BIG FFING MISTAKE. These fittings are junk and even with perfectly square and clean tube ends EVERY FITTING LEAKED. No matter what I did I could not get them to stop leaking - they are supposedly rated for the pressures in my application(my system runs no higher than 135psi), yet they just wouldn't seal. So, opted for flares the second time around. Home Depot was kind enough to refund all of my money for the crappy Watts fittings and the copper tubing that was unavoidably wasted.
My total investment in all of the parts is probably around $250, maybe a bit less. However, the entire point of having a good air compressor is being able to use it - excess water in the system was making it difficult to fully utilize the benefits of my machine
***
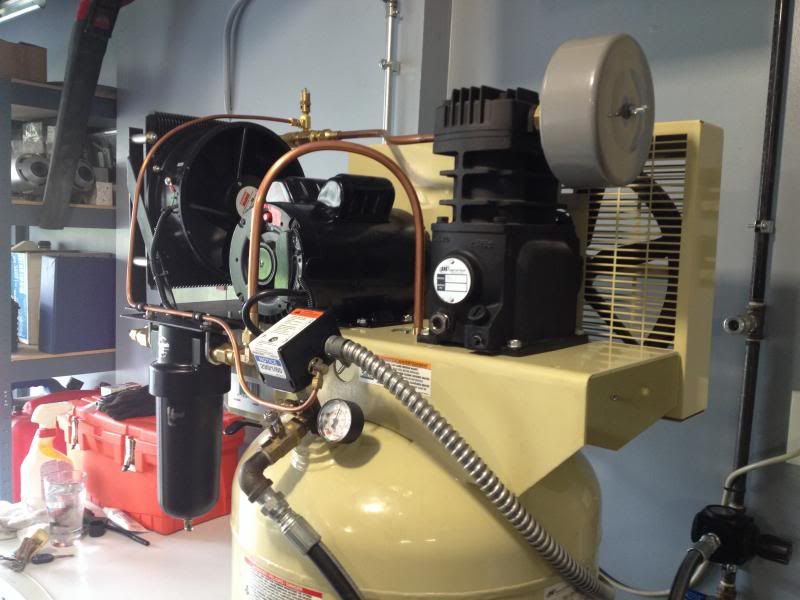
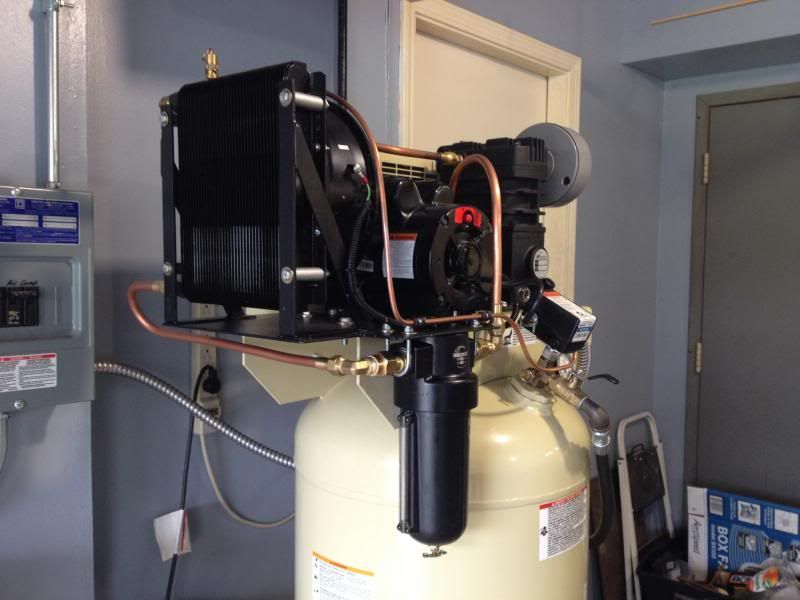
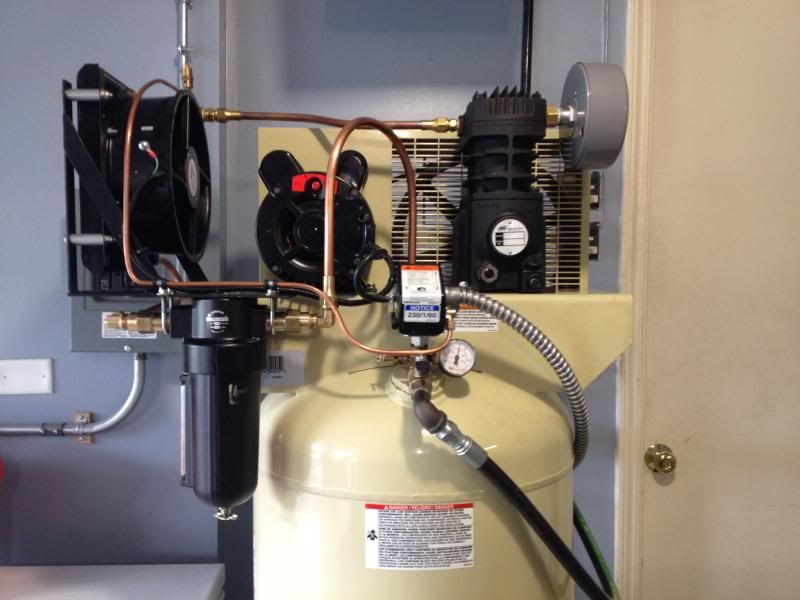
Comment